Discover expert fire pump maintenance tips to ensure safety and efficiency. Learn how to keep your system in top shape. Think of this: A tall structure catches fire, but the fire pump fails to turn on. Water pressure is insufficient to ascend the higher stories. The fire travels and does a lot of preventable harm. Sounds horrible, correct? This is the reason the upkeep of fire pumps is absolutely essential.
Effective operation of sprinkler systems during an emergency depends critically on fire pumps. Should they be neglected, they may fail when most needed. How, therefore, can you ensure that your system remains in a flawless state? Let’s explore some professional advice to maintain the best possible shape of your fire pump.
Understanding Fire Pump Maintenance
Let us first define exactly what a fire pump accomplishes before we go over maintenance ideas. Part of fire prevention systems, fire pumps raise water pressure as needed. Large buildings, industrial sites, and locations where water supply pressure is inadequate for firefighting demands all have them.
Fire pumps need frequent maintenance, just as any mechanical system does. They could have low pressure, leakage, or total failure without regular maintenance. Regular maintenance guarantees these pumps operate consistently in case of an emergency.
Maintenance also guarantees that fire suppression systems run at maximum performance during crucial events, therefore preserving their efficiency. Delayed response times resulting from inadequate maintenance of a pump might have disastrous results.
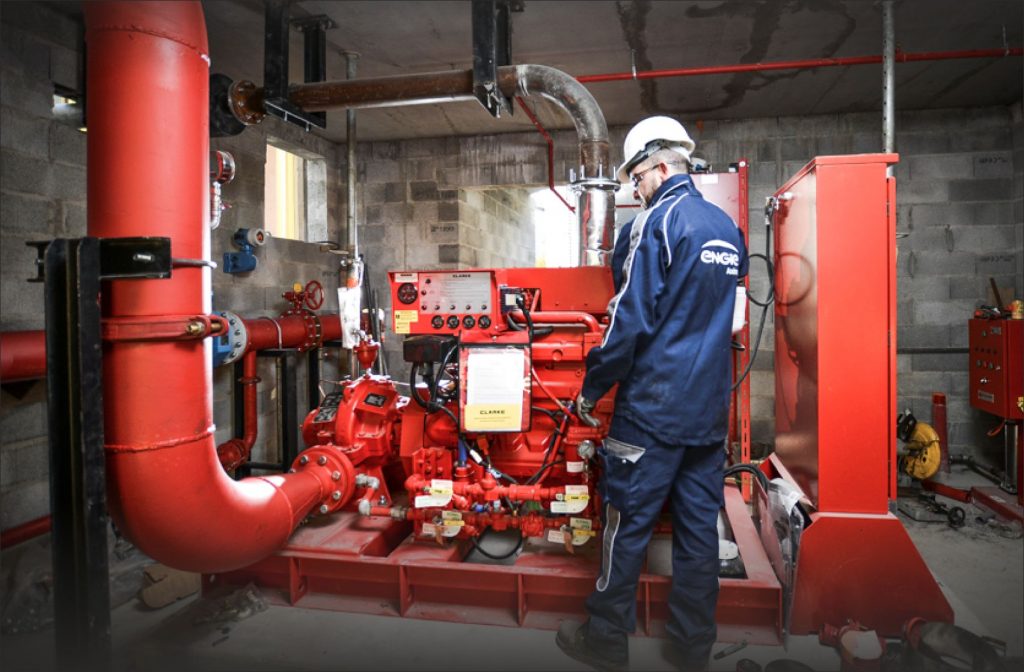
Benefits of Regular Fire Pump Maintenance
Ignoring fire pump maintenance could cause disastrous breakdowns. Regular maintenance has numerous main advantages:
- Reliability makes sure the pump turns on during a fire.
- Longevity: Increases the equipment’s lifetime.
- Many construction rules call for routine inspections in legal compliance.
- Prevents expensive emergency repairs and replacements, therefore saving money.
- Improved safety guard’s occupants and lowers property damage risk.
Weekly Fire Pump Inspections: What to Check
Regular inspections enable the identification of little problems before they become major ones. You should look at these once a week:
1. Visual Inspections
- Look for obvious leaks in the pump housing, valves, and pipelines.
- Inspect metal parts for rust or corrosion.
- Make sure operation produces no odd sensations or noises.
2. Pressure Gauges
- Track discharge pressure readings as well as suction.
- Make sure the readings stay within the advised range.
- Check any unexpected pressure declines with Pressure Gauges.
3. Pump Room Conditions
- Maintaining the area free of obstacles means keeping it clean.
- Monitor temperature; pump rooms should be above 40°F to avoid freezing.
- Look at electrical connections for damage or overheating indicators.
Monthly Fire Pump Maintenance ProTips
Apart from regular inspections, a more thorough monthly review guarantees all systems run as they should. You must accomplish the following:
1. Operate the Pump
- To guarantee flawless operation, run the pump for a minimum of ten minutes.
- Look for overheating, too much vibration, or unusual sounds.
- Check to be sure the pump begins automatically as needed.
2. Battery and Power Supply
- Examine battery terminals for corrosion.
- Check functionality by testing emergency power backup.
- Check that the controller is running continuously without interruptions of power.
3. Lubrication and Cooling System
- Verify the pump motor’s oil level.
- Verify bearings’ lubrication levels.
- Look over vents and cooling fans for obstructions.
Annual Fire Pump Maintenance: Professional Inspections
For compliance and safety, annual expert inspections are very necessary even though regular self-checks help. A qualified technician should check the following:
1. Full Performance Testing
- To confirm performance, run the pump fully.
- To guarantee correct pressure, check water flow rates.
- Point up any mechanical problems or efficiency losses.
2. Electrical and Mechanical System Inspection
- Look at connections and wiring for wear and tear.
- Look at pump seals for cracks or leakage.
- See how the pump and motor hookups line up.
3. Fire Alarm and Safety System Integration
- Make sure the fire pump fits the alarm system of the building exactly.
- Test sensors and automated start systems.
- Check that pressure switches turn on as intended.
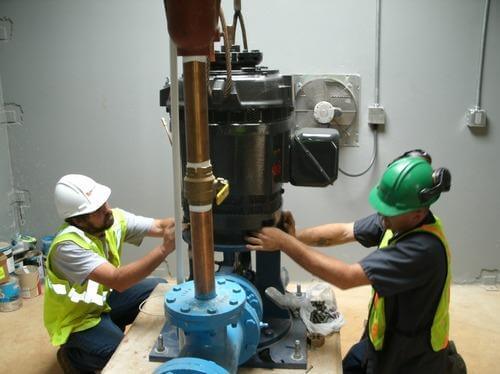
Common Fire Pump maintenance Issues and How to Fix Them
Fire pumps may have issues even with routine maintenance. These are many typical problems, together with solutions:
1. Low Water Pressure
- Possible cause: Potential causes include system air trapped in clogged filters or leaking valves.
- Solution: Bleed the air; change or clean filters; check for leaks
2. Overheating
- Possible cause: Potential causes include inadequate lubrication, blocked cooling vents, or too much friction.
- Solution: Lubricate sliding components, clear obstacles, and look for misalignment.
3. Unresponsive Motor
- Potential causes are battery problems, blown fuses, or electrical failure.
- Solution: Check and replace broken electrical components; test backup power; make sure the battery is charged.
4. Corrosion and Rust
- Possible causes could include a lack of protective coating and dampness.
- Solution: Treatments for corrosion should be routinely applied; keep the pump in a dry, temperature-regulated chamber.
A Real-Life Fire Pump Failure Story
Allow me to quickly provide a real-life illustration. Once ignoring monthly fire pump maintenance for more than a year, a facilities manager The pump failed from a clogged intake when a minor fire started. Firefighters came in time, so thankfully, but the property suffered major damage. This event emphasizes the need for regular maintenance inspections.
Following a periodic maintenance schedule would have helped prevent this expensive error. Frequent fire pump inspections can help to distinguish between a controlled event and a full-fledged disaster.
Best Practices for Fire Pump Maintenance
In essence, these are the finest strategies to make sure your fire pump stays in perfect shape:
- Look for early damage via weekly visual examinations.
- Test power supply and pump performance once a month.
- Plan yearly professional examinations to find unseen problems.
- Record all maintenance and test findings exactly.
- Staff should be taught correct fire pump operation as well as emergency procedures.
- Always have a backup for unanticipated breakdowns.
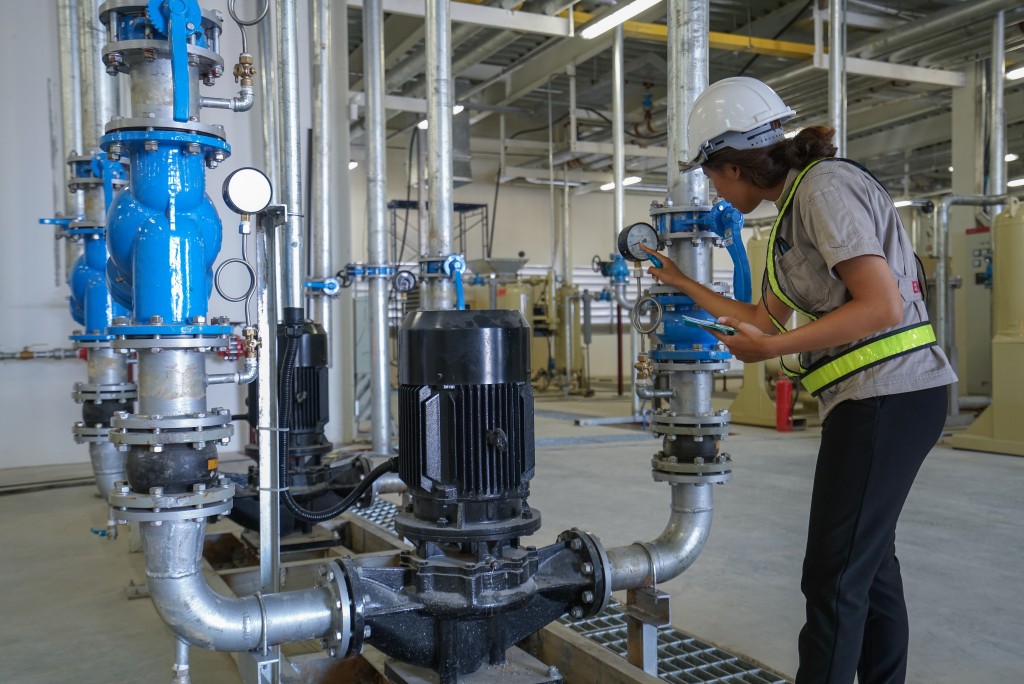
Conclusion: Stay Safe with Proper Fire Pump Maintenance
Maintenance of fire pumps is not only a technical obligation but also a lifesaver duty. When calamity hits, regular inspections, routine tests, and skilled servicing help to maintain your system dependable. Little work now will help to stop significant losses tomorrow.
Call to Action: Have you this month checked your fire pump maintenance list? Plan a check right now to maintain the safety of your structure! Read more…>>>